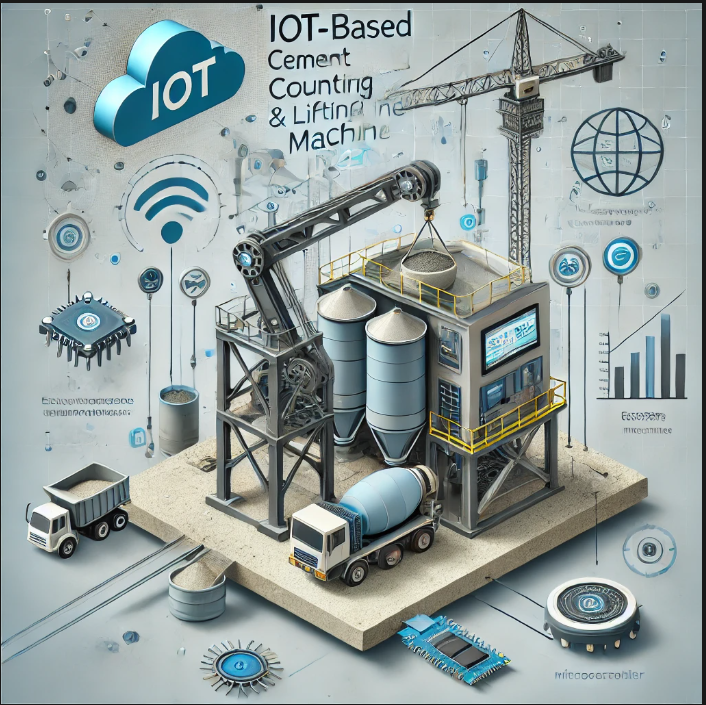
IoT-Based Cement Counting and Lifting Machine
The IoT-Based Cement Counting and Lifting Machine is a proposed solution designed to automate the cement lifting process, accurately track the number of lifting cycles, and differentiate between mixed and unmixed cement. By integrating this system with real-time monitoring through an ESP32 microcontroller, DC motors, and a water sensor, the solution will improve efficiency, reduce labor costs, enhance safety, and provide transparent data on cement usage
System Components and Functions
1. Microcontroller (ESP32)
- Role: Acts as the core control unit that manages inputs from sensors, limit switches, and cloud communication while controlling the DC motor.
- Project Context: The ESP32 processes data from the water sensor to detect mixed/unmixed cement, counts lifting cycles, and sends this data to the cloud for real-time monitoring and record-keeping.
2. Supply
- Role: Provides power to the microcontroller, DC motor, and other components.
- Project Context: Ensures reliable operation of the cement lifting machine by supplying consistent power.
3. DC Motor
- Role: Drives the lifting mechanism for the cement.
- Project Context: Automates the physical lifting of cement bags or containers. The motor's operations are controlled by the microcontroller based on inputs from limit switches and water sensors.
4. Water Sensor
- Role: Detects the presence of water to differentiate between mixed and unmixed cement.
- Project Context: The sensor determines whether the cement is in a mixed state, providing critical data for monitoring.
5. Limit Switches (Up and Down)
- Role: Detect the extreme positions of the lifting mechanism.
- Up Limit Switch: Indicates when the mechanism has reached the top position.
- Down Limit Switch: Indicates when the mechanism has reached the bottom position.
- Project Context: Helps the microcontroller count the number of lifting cycles accurately and ensures safe operation by preventing overtravel.
6. Cloud
- Role: Acts as the central hub for storing and accessing data remotely.
- Project Context: Facilitates real-time monitoring of cement lifting cycles, state (mixed or unmixed), and operational status via a dashboard.
7. Interface (Dashboard)
- Role: Displays data and system status to the user.
- Project Context: Provides a user-friendly interface for monitoring key metrics like lifting cycles, cement state, and operational errors, enhancing transparency.
System Workflow
- Initialization:
- The microcontroller initializes all components, including the motor, sensors, and limit switches.
- Cement Lifting:
- The DC motor activates to lift cement.
- Limit switches track the position of the lifting mechanism (up or down).
- The microcontroller counts each completed lifting cycle.
- Cement State Detection:
- The water sensor determines if the cement is mixed or unmixed during lifting.
- Data Transmission:
- The ESP32 microcontroller sends lifting counts, cement state, and operational data to the cloud.
- Real-Time Monitoring:
- The cloud updates the dashboard in real-time, allowing users to view system status and performance metrics.
- Automation and Safety:
- The system operates autonomously, with limit switches ensuring safe operation by stopping the motor at appropriate positions.
Advantages of the System
- Efficiency: Automates cement lifting, reducing the need for manual labor.
- Safety: Prevents accidents through precise motor control and limit switch mechanisms.
- Transparency: Tracks and displays cement usage, lifting cycles, and cement state.
- Real-Time Monitoring: Provides real-time operational data accessible remotely.
- Cost Reduction: Reduces labor costs through automation.
Components Required
- ESP32
- DC motor
- Limit switch
- Power supply
- Water sensor
- Web App
For More Information
+250783159293